To build a sustainable, clean energy economy that benefits all Americans, the Office of Energy Efficiency and Renewable Energy (EERE) utilizes applied research, development, demonstration, and deployment programs to bring down the cost of renewable, green, and Earth-friendly energy to parity with conventional energy sources.
Electrifying the Way to Lower Emissions
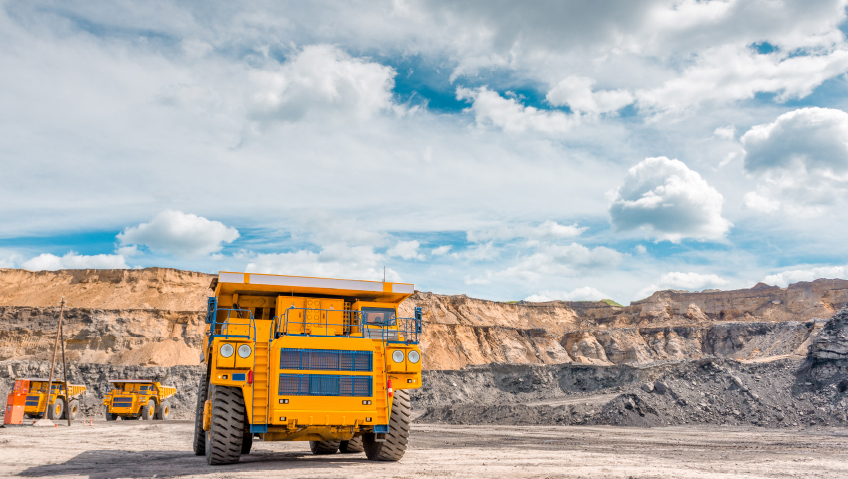
Once thought of as something from the future, electric vehicles (EVs) are now here to stay. While rechargeable batteries are nothing new and can be found in everything from smartphones to handheld drills, vast improvements in technology have made rechargeable batteries lighter and smaller, yet with the strength to power mining trucks and other heavy stuff. Batteries that seemingly took forever to charge and with little operating time are yielding to batteries with much shorter charging times, longer-lasting charges, and better lifespans.
Researchers and inventors have experimented with different batteries, some more successful than others. In 1859, French physicist Gaston Planté devised the lead-acid battery. Although he didn’t invent it—that honour goes to Wilhelm Josef Sinsteden just five years earlier—Planté improved on the original by adding extra plates, making the battery commercially viable.
Pioneering technology
Building on Sinsteden’s and Planté’s work, others made improvements to lead-acid batteries. One of them was Camille Alphonse Faure. A French chemical engineer, Faure increased the capacity of batteries. This not only saw lead-acid batteries begin to be made on a large scale in 1881, but it was the beginning of the rechargeable batteries used in automobiles. Versions of this battery are still being used in cars today.
Continuing to evolve, rechargeable batteries, as compared to their single-use cousins, are meant to be charged, discharged, and recharged again and again. Over time, various versions have emerged, including nickel-cadmium (NiCd), nickel-metal hydride (NiMH), lithium-ion (Li-ion), and many others.
As Li-ion, NiMH, solid-state batteries (SSB), and other types of rechargeable batteries gain popularity because of their energy efficiency, users are also benefiting from lower discharge levels, increased range, faster charging, and other considerations.
Reducing emissions
In a similar way to what’s happening in the auto sector with EVs, the resource sector, mining in particular, is turning away from equipment powered by diesel or other fossil fuel, and moving toward rechargeable battery power.
A key reason for the shift is pollution. Unlike gas-fueled trucks, mining drills, and other equipment, battery-powered vehicles do not spew greenhouse gas emissions (GHG) like carbon dioxide (CO2), methane (CH4), and nitrous oxide (N2O) into the atmosphere, contributing to global warming.
While there is always the counter-argument to be made by citing the mining of minerals for EC batteries like lithium, nickel and cobalt itself being responsible for GHG, the numbers of electric vehicles continue to grow. Worldwide, mining companies and others in the resource sector are embracing electrification to slash harmful CO2 emissions. One such mining site is the Jansen Potash Project. Located about 140 kilometres (87 miles) east of Saskatoon in Saskatchewan, the project is slated to “be one of the world’s largest and most sustainable potash mines,” according to multinational mining, metals, and natural gas petroleum giant BHP.
Last year, Normet Canada was awarded a contract from BHP for the delivery of an extensive fleet of multi-use, battery-electric vehicles (BEV) for the Jansen project. A leader in innovative technology, Normet’s offerings include underground mining and tunnelling services and equipment, chemicals for construction and Tunnel Boring Machines (TBMs), rock reinforcement, products, and more.
“BHP aims to develop the underground mining equipment and automation solutions with a focus on sustainability,” says Normet in a media release.
“Emissions reduction, improved productivity and advanced health and welfare of employees were key inputs to BHP Jansen’s decision to adopt BEV technology. With the mine’s pursuit of electrification of mobile equipment and technology that mitigates natural gas emission, Janseni will emit about half the average CO2 per tonne of product compared to the average Saskatchewan potash mine.”
In other words, through the use of these heavy-duty EVs, CO2 emissions on the Jansen site will be reduced by 50 percent compared to the average.
Delivery of the new BEVs is slated to extend into 2024, with production set to commence in 2026. Considering that the Saskatchewan-based site is predicted to be in operation for a century, the purchase represents a bold step forward for electric vehicle technology in Canada.
Making the switch
One of the world’s largest mining, metals, and natural gas companies, BHP is far from alone in making the switch to electric vehicles and battery-powered equipment like drill rigs in the interests of decarbonization and sustainable development.
Backed by US$400 million in investment in its climate investment program, the company is actively working to lower its emissions, and on low carbon steelmaking. During the 2020 calendar year, the company’s investment in energy transition hit US$501.3 billion, the highest level to date—and switching to EVs represents a big part of BHP’s change.
“One of the mega-trends expected to shape our long-run operating environment is the electrification of transport,” says Dr. Huw McKay, Vice President of Market Analysis and Economics, on a section of the company’s website dedicated to the electrification of transport.
Two and a half years before the 2019 post, BHP spoke about the “bullish outlook for electric vehicles,” which slowed for a time because of COVID-19. Although delayed by the pandemic, BHP and many other resource-sector companies are back on track in their pursuit of electrification.
Mine sites worldwide, especially underground operations, continue investing in EVs and battery-powered machinery to lower their carbon footprint. In 2022, analytics and consulting company GlobalData Plc detailed the rise in mining investment in electrification as the industry transitions to cleaner technologies.
This includes the presence of 157 electric loaders (LHDs) and 45 electric trucks operating in the world’s underground mines, in locations including Canada, Russia, Sweden, and Australia, an increase of 20 from 2021.
Newly formed Agnico Eagle Mines Limited (a merger of Kirkland Lake Gold and Agnico Eagle) reportedly had the most LHDs and trucks in operation with 49 (combined), “including 27 battery or electric-powered LHDs and 17 battery-powered underground mining trucks at its Macassa mine in Canada,” says GlobalData.
The rising popularity of EVs in underground mine operations is fully justified. Electric vehicles not only reduce greenhouse gases, but they are quieter than their diesel-powered counterparts, do not run as hot, and have fewer parts than traditional equipment. Especially important are the health and safety benefits.
Regular diesel engines produce significant quantities of noxious gases and submicron aerosols, including CO2, CO, NOX and hydrocarbons (HC). To counteract these gases and the exposure of workers to them in underground mines, costly ventilation systems are needed to increase the flow of air, dilute harmful gases, reduce dust, and regulate temperature.
Providing electricity to power these ventilation systems is a significant expense for mine operators. In the Hard Rock Miner’s Handbook, author Jack de la Vergne wrote, “The highest operating cost to provide contemporary mine ventilation is the electrical energy for the fans, which typically represents more than one-third of the entire electrical power cost for a typical underground mine.”
Since EVs operating underground don’t create harmful emissions, about 40 to 50 percent less ventilation is required, and the power that would be used for ventilation can instead charge EVs and equipment.
Mining and resource sector companies, large and small, are embracing EVs for their reliability, safety, and drastically reduced emissions compared to diesel-fueled vehicles. One of the world’s biggest mining companies, Glencore, placed an order last summer for battery-electric mining equipment from Sweden’s Epiroc, one of the country’s most prominent mining and infrastructure-equipment manufacturers.
The new fleet will be used at Glencore’s nickel and copper mine, Onaping Depth Project, in Ontario, Canada. “Glencore is taking a major leap forward in the mining industry by going all-electric with its Onaping Depth Project,” said Helena Hedblom, Epiroc’s President and CEO in a media release. “We’re excited to collaborate with Glencore and deliver battery-electric vehicles and automation features on their journey to build a mine of the future.”
164 years after Gaston Planté’ created the first practical electric storage battery, versions of his invention are ‘coming to power’ in every kind of vehicle everywhere. Undoubtedly, he would be pleased to see just how far his technology reaches today.
AUTHOR
CURRENT EDITION
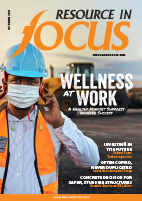
Wellness at Work
Read Our Current Issue
PAST EDITIONS
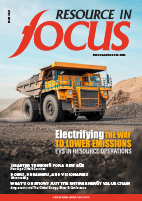
Electrifying the Way to Lower Emissions
May 2023
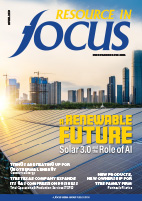
A Renewable Future
April 2023
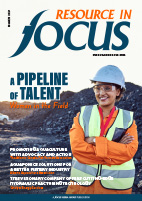
A Pipeline of Talent
March 2023
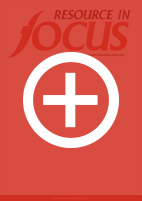